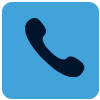

2020 官网升级中!现在您访问官网的浏览器设备分辨率宽度低于1280px请使用高分辨率宽度访问。
In the dynamic landscape of the dental industry, where the shift from labor-intensive to technology-intensive practices is evident, automation technologies are becoming increasingly essential. The utilization of 3D printing in the dental industry has brought about a transformative shift, offering numerous advantages that significantly impact efficiency, precision, and patient care.
1. Unparalleled Precision
• 3D printing excels in producing complex geometries and intricate designs, curves, holes, corners and small shapes are fine for 3D printers.
• Minimum wall thickness for 3D printing RPDs can be reduced to 0.3mm compared to 0.6mm achieved by traditional casting.
• Manual errors, often a concern in traditional methods, are effectively avoided. The defect rate has been reduced to 0.8% according to our experience.
2. Faster Turnaround
• The conventional steps involving waxing, embedding, casting, and extensive contouring could be eliminated. Chamlion’s M150 metal 3D printer can 210 crowns or 13 partial frameworks in less than 5 hours.
• The utilization of 3D printing technology not only streamlines the production process but also the preparation and design. Dental technicians can work with digital data records which are transmitted to dental laboratories in real time. There are no plaster casts or silicone imprints.
3. Less material, reduced waste
• In the conventional method, dental technicians first create the basic shape and then hollow it out. This means that up to 80 percent of the material ends up being thrown out.
• 3D printer only processes as much metal powder as it actually needs. This not only saves you money, it also benefits the environment.
• Efficient nesting of multiple parts within a single build, optimizing the use of space and minimizing unused material.
4. Broad Versatility and Compatibility
• 3D printing allows the exploration of a wide range of materials, such as CoCr and Titanium, providing flexibility in material selection for various dental applications.
• Titanium possesses both hardness and biocompatibility. However, due to the substantial material waste associated with milling-based processing, the cost becomes prohibitively high, and casting becomes highly impractical.
• A wide range of dental applications can be manufactured by 3D printers such as RPDs, C&Bs, and ALL-ON-X.
5. Enhanced Patient Experience
• The precise fit of 3D-printed dental prosthetics enhance the overall patient experience. Reduced chairside adjustments and improved comfort contribute to increased patient satisfaction and confidence in dental treatments.
• 3D printing enables the creation of customized and patient-specific structures with ease.